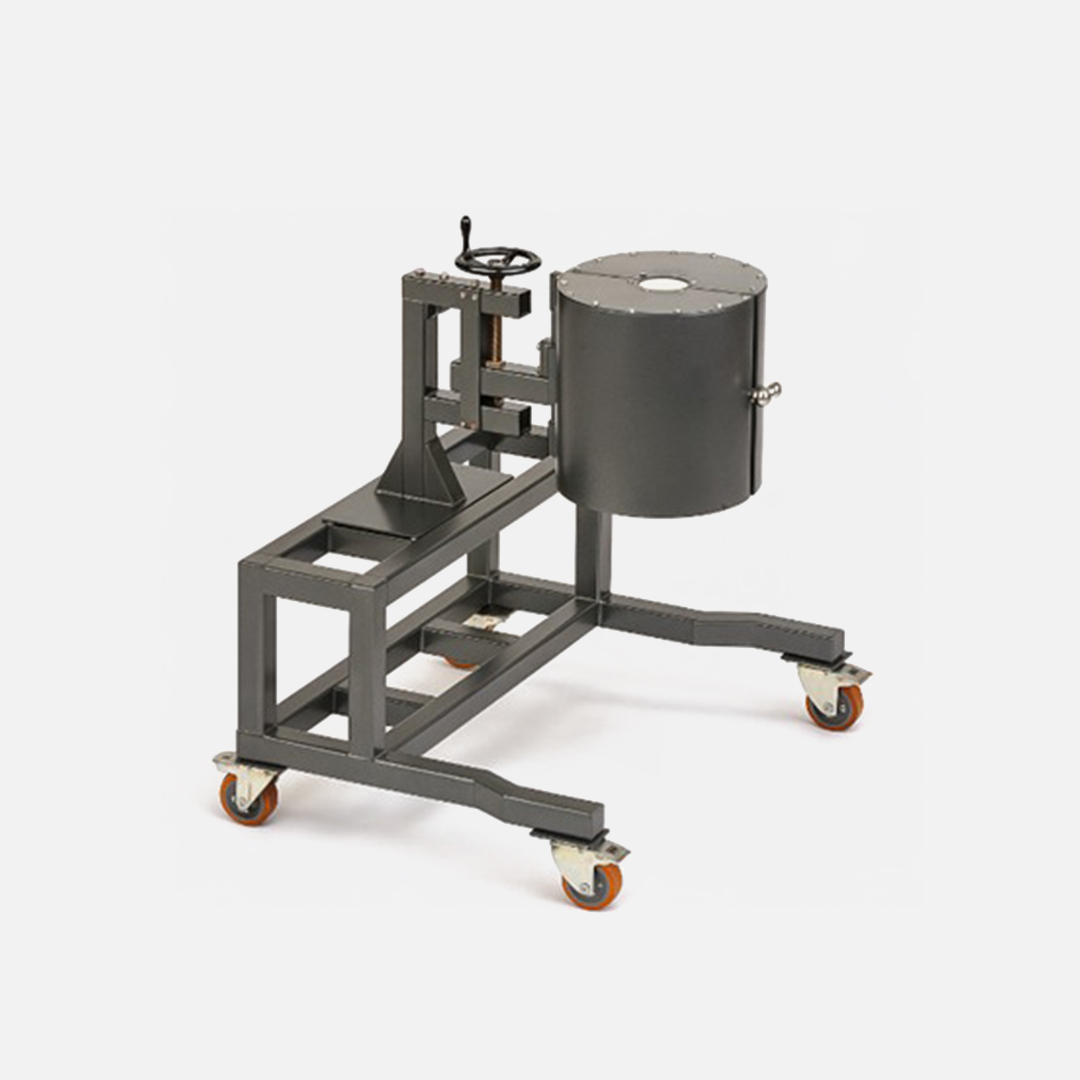
Split Tube Furnace for UTM
The Split Tube Furnace for Universal Testing Machines (UTM) is engineered for in-situ high-temperature mechanical testing—enabling tensile, compression, or creep tests under controlled thermal conditions. Designed to seamlessly integrate with most UTMs, it allows researchers and quality engineers to analyze material behavior at elevated temperatures with exceptional accuracy and repeatability.Â
This furnace is an essential tool in materials science, metallurgy, ceramics, and aerospace R&D, providing real-time insight into mechanical deformation, failure modes, and performance under thermal stress.Â
Typical Configuration
- Heating Zones: 1–3 zones (customizable)Â
- Sample Chamber: Custom openings for extensometers and gripsÂ
- Controller: Touchscreen PID with real-time monitoring and safety interlocksÂ
- Mounting: Adaptable brackets for most vertical and horizontal UTM framesÂ
Key Features
Applications
Optional Features
Key Features
- Temperature Range: Ambient to 1600°CÂ
- Multi-Zone Heating: Ensures uniform temperature distribution across the gauge lengthÂ
- Split-Hinge Design: Easy clamshell-style access for rapid sample loading and removalÂ
- Compact & UTM-Compatible: Designed to fit seamlessly with standard test setupsÂ
- Fast Ramp Rates: Enables efficient thermal cycles during material testingÂ
- Sample Holder Flexibility: Supports a range of grip styles and sample geometriesÂ
- Insulation: High-performance ceramic fiber insulation for energy efficiency and safetyÂ
- Accurate Control: PID temperature control system with programmable ramp/hold profilesÂ
Applications
- High-Temperature Tensile & Creep TestingÂ
- Compression Testing of Ceramics & CompositesÂ
- Thermo-Mechanical Characterization of Metals & AlloysÂ
- Validation of Structural Materials for Aerospace & AutomotiveÂ
- Thermal Cycling Studies for Fatigue ResistanceÂ
Optional Features
- Quartz or alumina inner liners for atmosphere-sensitive testingÂ
- Viewing ports for optical/video monitoring during testÂ
- Inert gas flow system for oxidation-free testingÂ
- Data logging and PC interface for synchronized UTM + furnace dataÂ