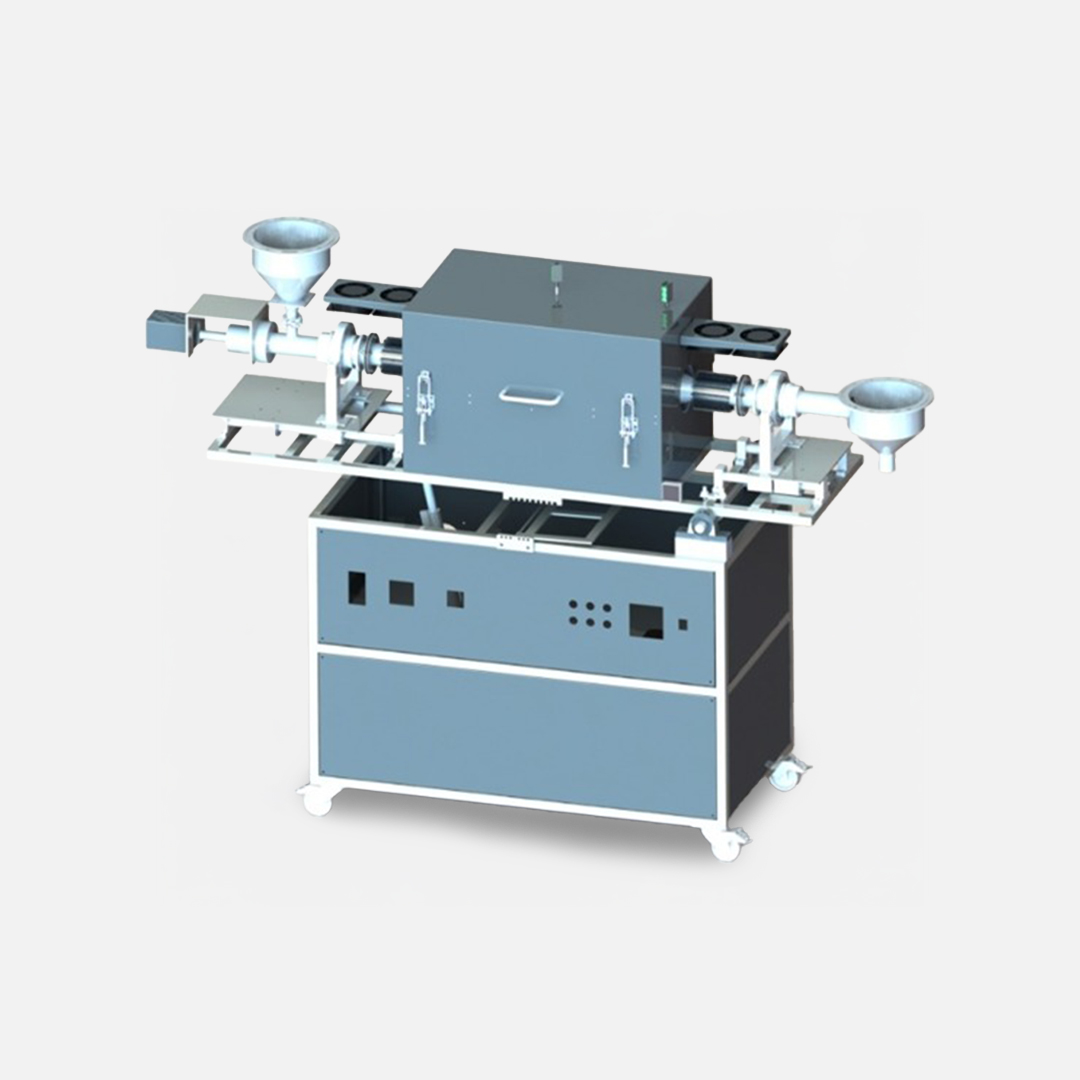
Rotary Tube Furnace
A Rotary Tube Furnace is a cylindrical, rotating high-temperature system designed for continuous or semi-continuous thermal treatment of materials. Commonly used in chemical synthesis, metallurgy, ceramics, ore roasting, and recycling, it ensures uniform temperature exposure and efficient material movement—ideal for processes like calcination, sintering, metal recovery, and reduction reactions.Â
By rotating the tubular chamber during heating, the system enhances material mixing, improves thermal contact, and ensures consistent process conditions, even at elevated temperatures up to 1300°C.Â
Typical Configuration
- Tube Diameter: 100 mmÂ
- Usable Length: ~300 mmÂ
- Usable Volume: Approx. 1–3 litersÂ
- Rotary Drive: DC motor with gear assembly for precise motion controlÂ
Key Features
Applications
Optional Features
Key Features
- Temperature Range: Up to 1300°C for high-temperature processingÂ
- Rotary Motion: 0–10 RPM adjustable rotation for uniform heating and material agitationÂ
- Heating Zone: 600 mm total hot zone with a uniform 300 mm heating sectionÂ
- Tube Material: Inconel 600 retort (resistant to oxidation, carburization, and corrosion)Â
- Insulation: Non-carcinogenic fiber insulation with Kanthal A-1 heaters mounted on mullite tubesÂ
- Construction: Dual-body steel housing with anti-corrosion coating and fan-cooled bodyÂ
- Control System:Â
- PID programmable controllerÂ
- K-type thermocouple (Inconel-sheathed)Â
- Solid-state relay (SSR) based power controlÂ
- Atmosphere Compatibility: Operates under inert or reactive gases including Ar, Nâ‚‚, He, Oâ‚‚, COâ‚‚, and Hâ‚‚ blendsÂ
- Pressure Rating: Maintains internal pressures up to 70 mbarÂ
- Feed & Discharge System: Screw feeder and hopper for continuous, atmosphere-controlled material loading/unloadingÂ
Applications
- Material Synthesis: Solid-state reactions under controlled environmentsÂ
- Ore Roasting & Metallurgical ProcessingÂ
- Lead and Aluminum Recycling: Especially with tilting rotary optionsÂ
- Ceramic Sintering & CalcinationÂ
- Cement Clinker ProductionÂ
- Catalyst Preparation and Chemical Reaction EngineeringÂ
- Pyrolysis and Gas-Solid Reaction StudiesÂ
Optional Features
- Multi-zone temperature controlÂ
- Tilting mechanism for enhanced metal recoveryÂ
- Real-time data logging & SCADA integrationÂ
- Quartz or ceramic tubes for specific chemical environmentsÂ