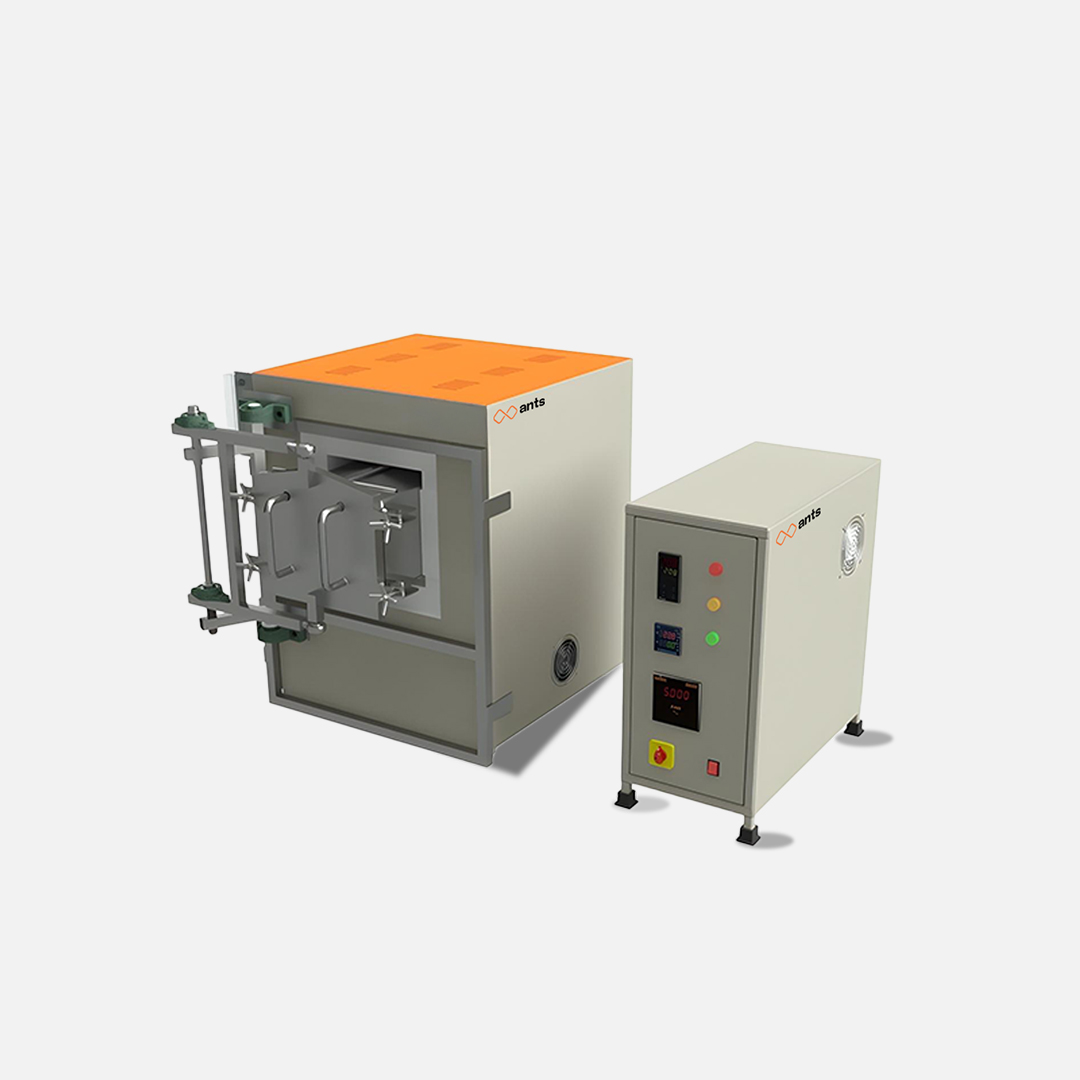
Retort Furnace
A retort furnace is a specialized high-temperature thermal processing system designed for heat treatment of materials in a sealed, controlled atmosphere. Its cylindrical or rectangular retort (chamber), which is composed of ceramics or heat-resistant alloys, keeps the sample away from the heating components and outside air. Because of its architecture, it is perfect for procedures like brazing, sintering, annealing, and degassing that call for a clean, inert, or reducing atmosphere. Because of their accuracy, consistency, and capacity to regulate the atmosphere, retort furnaces are extensively utilized in metallurgy, electronics, and advanced material research.
A retort furnace is a specialized high-temperature thermal processing system designed for heat treatment of materials in a sealed, controlled atmosphere. Its cylindrical or rectangular retort (chamber), which is composed of ceramics or heat-resistant alloys, keeps the sample away from the heating components and outside air. Because of its architecture, it is perfect for procedures like brazing, sintering, annealing, and degassing that call for a clean, inert, or reducing atmosphere. Because of their accuracy, consistency, and capacity to regulate the atmosphere, retort furnaces are extensively utilized in metallurgy, electronics, and advanced material research.
- Sealed Retort Chamber: Ensures contamination-free processing by isolating the sample from external gases and heating elements.
- Controlled Atmosphere: Supports inert (argon, nitrogen), reducing (hydrogen), or vacuum environments for sensitive materials.
- Uniform Heating: Surround heating elements and thermal insulation provide consistent temperature distribution.
- Programmable Control: Microprocessor-based PID controller with ramp/soak profiles for precise thermal cycling.
- Durable Construction: High-grade alloy or ceramic retort with robust outer casing for long-term reliability.
- Brazing: Ideal for joining metals in a clean, controlled environment.
- Sintering: Used for densifying powdered metals and ceramics.
- Annealing: Suitable for relieving internal stresses in metals and alloys.
- Degassing: Removes volatile contaminants from materials under vacuum or inert gas.
- Heat Treatment of Reactive Materials: Enables safe processing of materials sensitive to oxidation or contamination.
- Temperature Range: 800 °C to 1300 °C (higher ranges available on request in cold wall configuration)
- Retort Size: 2 to 50 liters (custom sizes available)
- Retort Material: Heat-resistant stainless steel (SS310, SS316), Inconel, or high-alumina ceramic
- Heating Elements: Kanthal / SiC / MoSiâ‚‚
- Temperature Accuracy: ±1 °C
- Temperature Uniformity: ±3 °C across the chamber
- Controller: Digital PID with programmable ramp/soak profiles and over-temperature protection
- Insulation: Multi-layer ceramic fiber or refractory brick
- Atmosphere Control: Gas inlet/outlet ports with flow meters or mass flow controllers; optional vacuum system
     Retort furnaces can be customized with the following features:
- Retort Shape & Material: Cylindrical or box-type, based on application and temperature requirements.
- Gas Handling System: Integrated gas mixing, purging, and exhaust systems.
- Vacuum Compatibility: Optional vacuum pumps and sealing systems for low-pressure operations.
- Data Logging & Connectivity: USB, RS-485, or Ethernet for real-time monitoring and control.
- Software Integration: Compatible with lab automation and SCADA systems for remote operation and data analysis.
- Safety Features: Over-temperature protection, gas leak detection, and interlock systems.