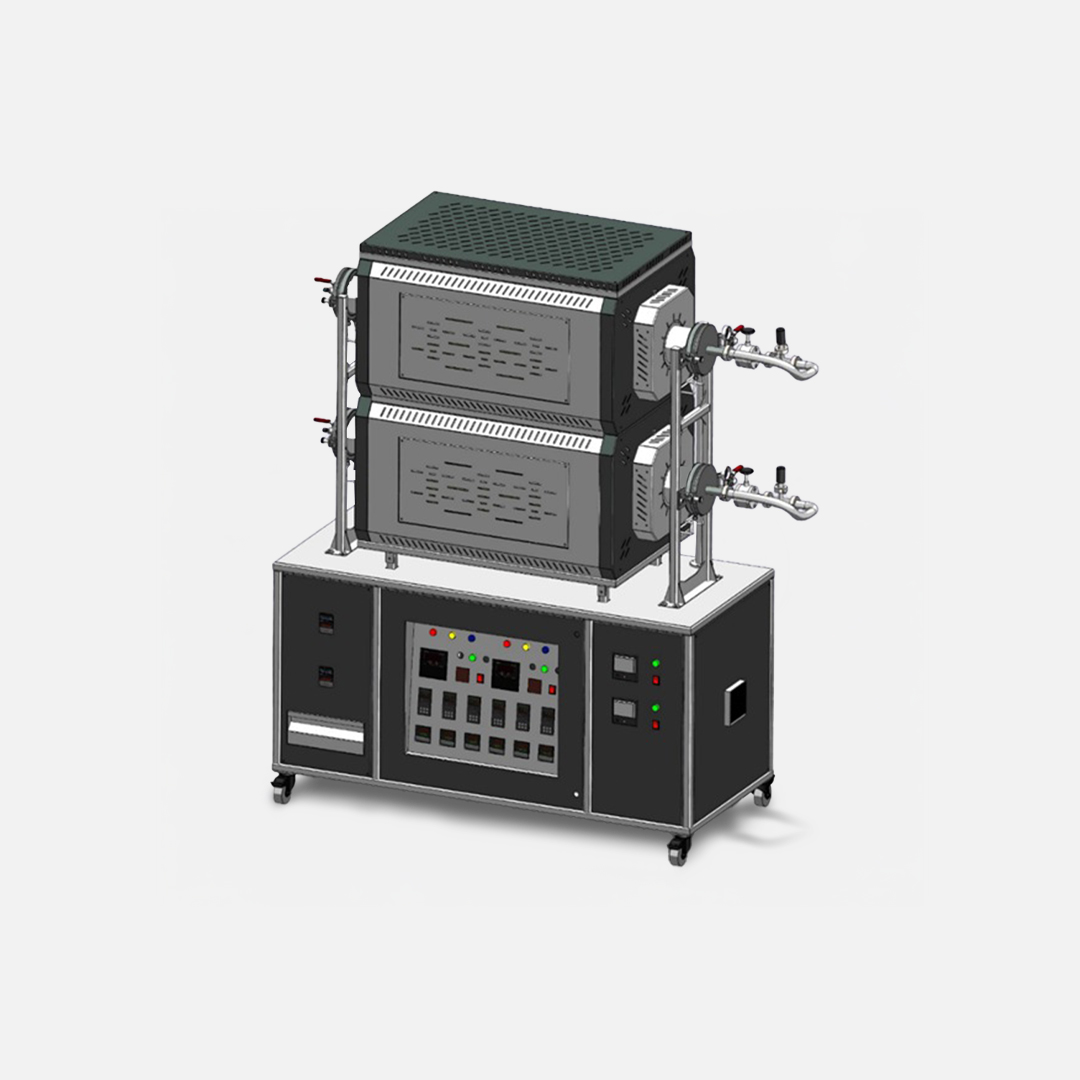
Oxidation & Diffusion Furnace
The Oxidation & Diffusion Furnace is a specialized high-temperature system used extensively in semiconductor device manufacturing, particularly for growing silicon dioxide (SiOâ‚‚) layers on silicon wafers. Designed for dry and wet oxidation as well as dopant diffusion processes, these furnaces offer high thermal uniformity, precise gas flow control, and repeatable process reliability.Â
Core Functions
- Oxidation: Formation of silicon dioxide layers for insulation, surface passivation, and gate dielectricsÂ
- Diffusion: Thermal activation of dopants like boron or phosphorus into the silicon substrateÂ
- Annealing: Post-implantation repair and dopant activationÂ
- Drive-In Processes: Further diffusion of pre-deposited dopants under controlled conditionsÂ
Operating Principle
Utilizing temperatures from 800°C to 1200°C, the furnace allows for
- Dry Oxidation: Pure Oâ‚‚ forms thin, high-quality oxide layers—ideal for gate oxidesÂ
- Wet Oxidation: Oâ‚‚ + Hâ‚‚O (steam) enables faster growth of thicker oxide layers—suitable for field oxidesÂ
The oxidation process follows the Deal–Grove model, where oxide growth is time and temperature dependent. Multiple wafers are processed uniformly in a quartz or silicon carbide reaction tube, supported by precise gas flow systems, automated wafer handling, and multi-zone heating.Â
- Temperature Range: 800°C to 1200°C with ±1°C uniformityÂ
- Tube Material: High-purity quartz or SiCÂ
- Gas Flow Control: Multi-channel MFCs for Oâ‚‚, Nâ‚‚, Hâ‚‚, and steam introductionÂ
- Wafer Handling: Manual or automated loading optionsÂ
- System Control: PLC/HMI with recipe programming and data loggingÂ
- Cleanroom-Compatible Design: Suitable for Class 100/1000 environmentsÂ
- Gate Oxide Growth for MOSFETsÂ
- Field Oxide Isolation (LOCOS process)Â
- Surface Passivation for Improved Device StabilityÂ
- Dopant Diffusion and Drive-In AnnealingÂ
- Masking for Photolithography and Etching ProcessesÂ
- Single or Dual Tube ConfigurationsÂ
- Integrated Steam Generators for Wet OxidationÂ
- Vacuum or Controlled Atmosphere ModesÂ
- Wafer Boat Designs for 2″, 4″, 6″, or 8″ wafersÂ
- Multi-zone Heating for Axial UniformityÂ