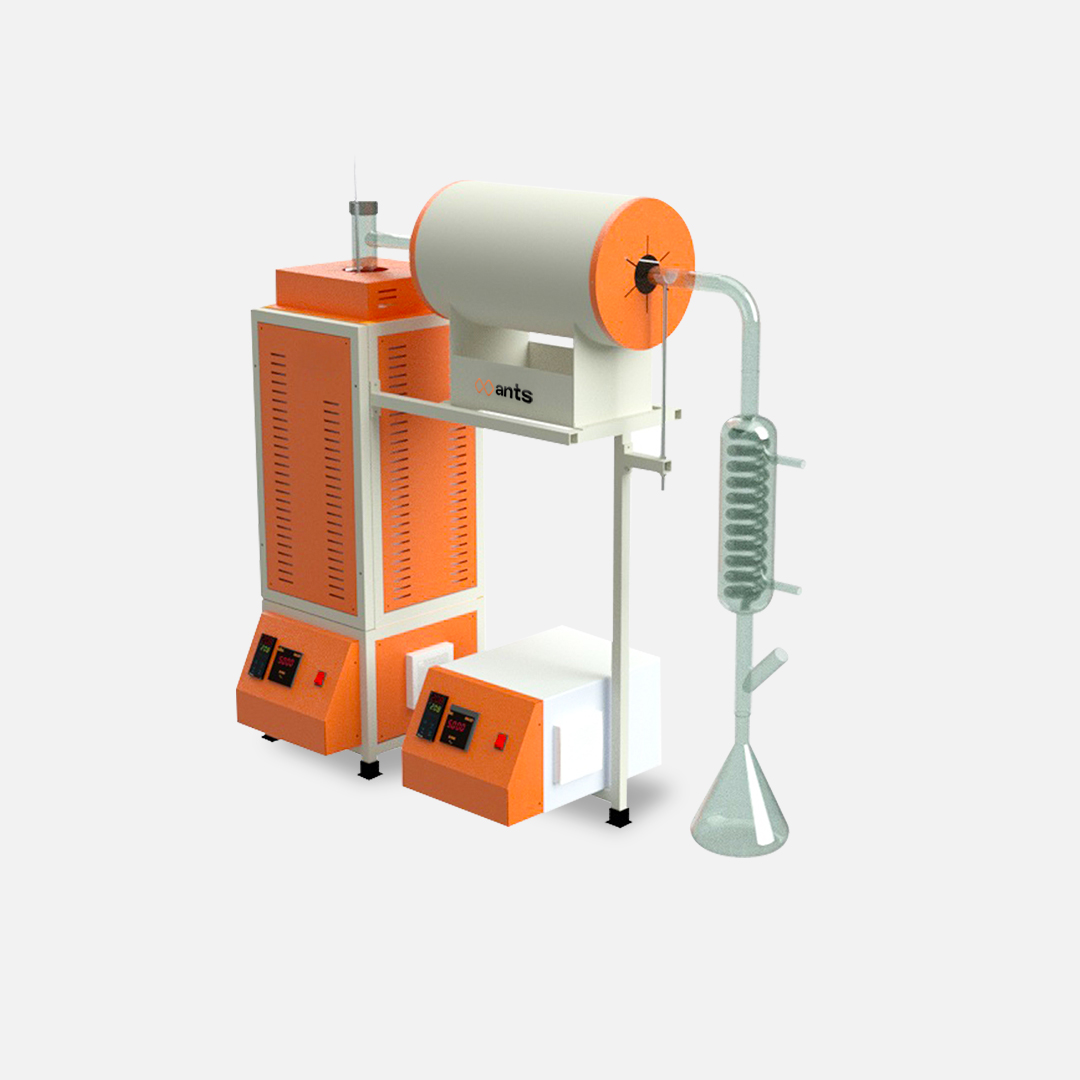
Fluidized Bed Furnace
A Fluidized Bed Furnace creates a fluid-like state by suspending solid particles in a uniform stream of gas, ensuring excellent heat transfer, precise temperature control, and homogeneous processing. Designed for applications ranging from ore beneficiation to thermal decomposition and combustion studies, this furnace is a versatile platform for industrial and research use.Â
How It Works
The furnace operates by introducing gas or air through a distributor plate at the base of a chamber filled with granular materials (e.g., sand, metal powders, or catalysts). This upward gas flow fluidizes the bed, turning the solid particles into a highly uniform, dynamic heat transfer medium. The result is an ideal environment for consistent temperature distribution, rapid heating, and excellent mixing.Â
- Operating Temperature: 750°C to 1600°CÂ
- Heating Method:Â
- Lab-Scale: Electrically heated external wallsÂ
- Industrial Scale: Compatible with solid, liquid, and gaseous fuels
- Gas Distribution: Precision-designed gas manifold and plenum for uniform pressure and flowÂ
- Temperature Uniformity: Superior due to constant mixing of bed particlesÂ
- Control Interface: Optional PLC/HMI with data logging and recipe programmingÂ
- Ore Beneficiation – Refractory-grade iron ore processingÂ
- Thermal Desorption & Pyrolysis – Treatment of waste or contaminated solidsÂ
- Calcination & Reduction – Of minerals and metal oxidesÂ
- Combustion Studies – Biomass, coal, or alternate fuelsÂ
- Material Coating & Surface Modification – Via vapor-solid interactionÂ
- Waste Incineration & Gasification – With emission controlÂ
- Efficient Heat Transfer – Due to continuous particle movementÂ
- Uniform Processing – Prevents hot spots or thermal gradientsÂ
- Fuel Versatility – Biomass, waste, low-grade coal, gasesÂ
- Compact, Scalable Design – Adaptable for pilot or production setupsÂ
- Lower Emissions – As compared to conventional combustion systemsÂ