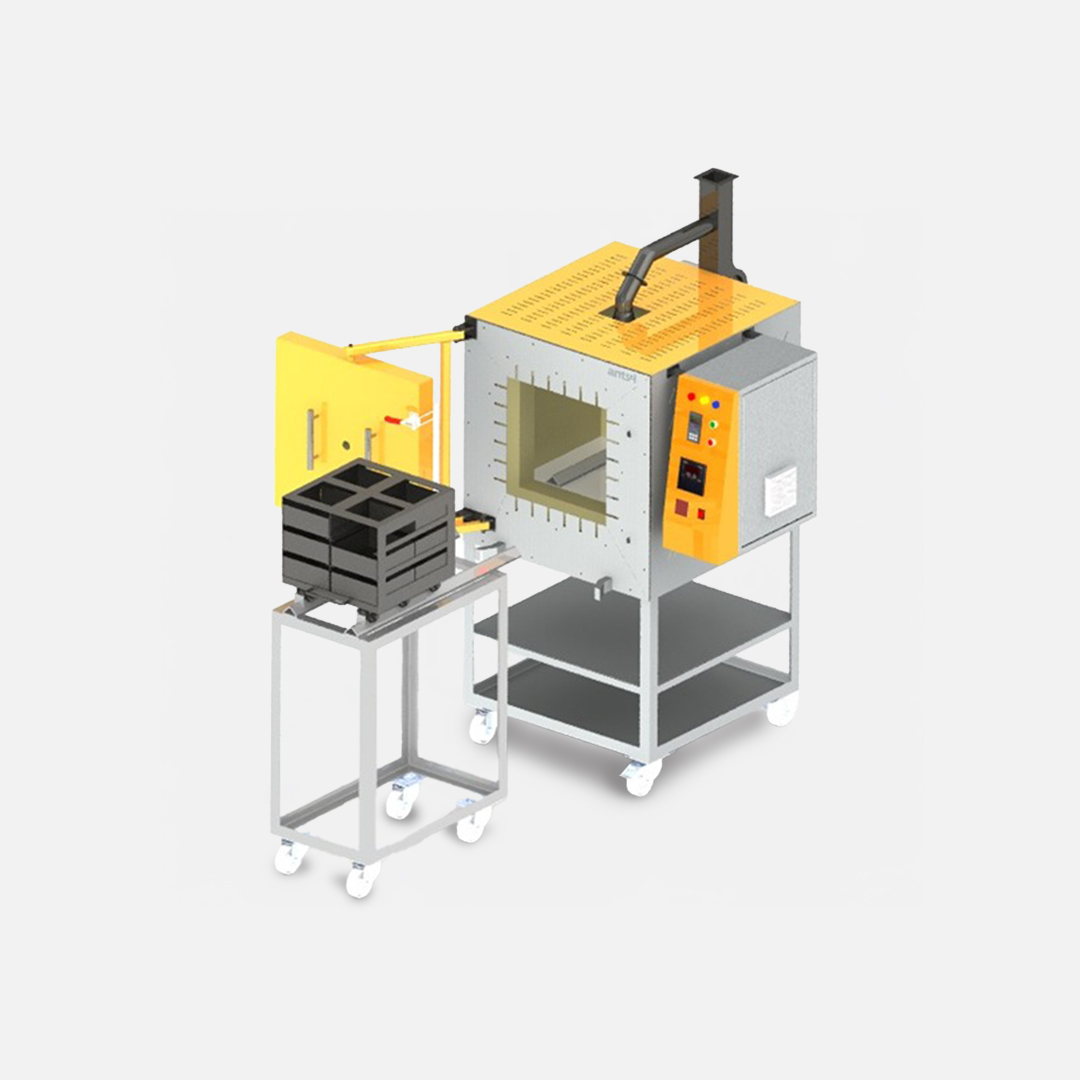
Calcination Kiln
A Calcination Kiln is a high-temperature thermal processing unit used for inducing thermal decomposition, phase transitions, oxidation, or sintering in solid materials. Typically operating between 550°C and 1150°C, these kilns are central to metallurgy, cement production, chemical synthesis, material recycling, and environmental remediation applications.Â
- Decomposition: Removal of volatile substances or chemically bonded water (e.g., converting CaCO₃ to CaO)Â
- Oxidation: Controlled combustion or oxygen-driven reactions in ores and catalystsÂ
- Sintering: Heat-based consolidation of powders for catalyst and ceramic productionÂ
- Roasting: Processing metal ores to convert sulphides to oxidesÂ
- Waste Treatment: Thermal neutralization or transformation of hazardous materialsÂ
1.Temperature Range: 550°C to 1150°C (customizable for application)Â
2.Heating Type:Â
Direct heating for general-purpose useÂ
Indirect heating (hidden heaters) for corrosive or toxic fume-generating materials
3.Atmosphere Control: Ambient air, inert gas, or controlled oxidative environmentsÂ
4.Material Handling: Options for automated loading/unloading, conveyor or batch operationÂ
5.Construction: High-grade insulation, corrosion-resistant internals, and thermally stable refractory liningÂ
6. Gas Exhaust System: Efficient flue design with filtration for harmful gases and particulatesÂ
7. Heater Protection: Hidden heater design prolongs life in corrosive and high-particulate environmentsÂ
- Cement & Lime Manufacturing: Conversion of limestone into quicklime (CaO)Â
- Catalyst Activation & SinteringÂ
- Ore Roasting in MetallurgyÂ
- Thermal Processing in Chemical SynthesisÂ
- Recycling of Industrial By-productsÂ
- Treatment of Toxic/Reactive Waste MaterialsÂ
- Gas scrubbing or fume filtration unitsÂ
- Data logging & temperature profiling via PLC/SCADAÂ
- Custom insulation systems for energy efficiencyÂ
- Advanced safety interlocks and alarmsÂ