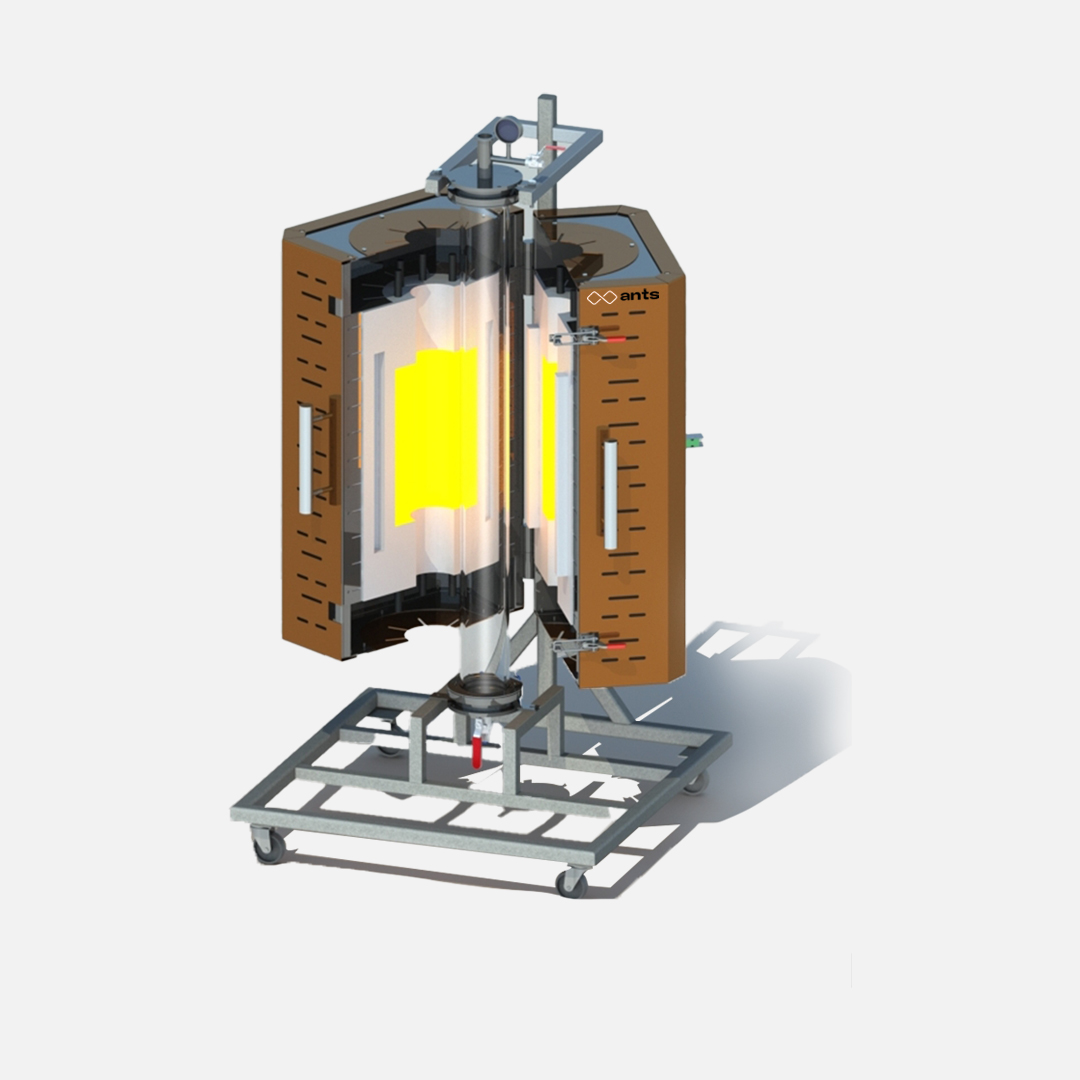
Vertical Tube Furnace
A vertical tube/split tube furnace is a type of high-temperature heating apparatus used to process samples vertically in a cylindrical tube. It is perfect for uses that need for regulated atmospheres, homogenous heating, gravity-assisted reactions like quenching and processes involving gas solid interactions like the ones in catalysis and fluidized bed reactions.
For procedures like crystal formation, vapor phase reactions, and thermal decomposition, the vertical arrangement makes it simple to load crucibles, boats, or sample holders from the top. The furnace is designed to be precise and dependable, with high thermal uniformity, sophisticated temperature control, and adaptable tube designs to suit a range of commercial and research requirements.
A vertical tube/split tube furnace is a type of high-temperature heating apparatus used to process samples vertically in a cylindrical tube. It is perfect for uses that need for regulated atmospheres, homogenous heating, gravity-assisted reactions like quenching and processes involving gas solid interactions like the ones in catalysis and fluidized bed reactions.
For procedures like crystal formation, vapor phase reactions, and thermal decomposition, the vertical arrangement makes it simple to load crucibles, boats, or sample holders from the top. The furnace is designed to be precise and dependable, with high thermal uniformity, sophisticated temperature control, and adaptable tube designs to suit a range of commercial and research requirements.
- Vertical Configuration: Facilitates gravity-driven processes and top-loading sample access, ideal for crucible-based reactions.
- Uniform Heating Zone: Optimized heating element placement ensures consistent temperature distribution along the tube length.
- Atmosphere Control: Supports inert, reducing, or oxidizing gas environments with optional vacuum compatibility.
- Programmable Control: Microprocessor-based PID controller with ramp/soak profiles for precise thermal cycling.
- Compact Footprint: Space-efficient design suitable for benchtop or floor-mounted setups.
- Crystal Growth: Ideal for vertical Bridgman or Czochralski methods.
- Vapor Phase Reactions: Supports chemical vapor deposition (CVD) and sublimation processes.
- Thermal Decomposition: Used for pyrolysis and breakdown of materials under controlled conditions.
- Material Synthesis: Suitable for gas solid-state reactions (catalysis, fluidized bed reactions, gettering) and nanoparticle production.
- Temperature Range: 1000 °C / 1200 °C / 1400 °C / 1600 °C
- Tube Diameter: 25 mm to 100 mm
- Tube Length: 300 mm to 1000 mm
- Tube Material: Quartz / Alumina / Inconel / SiC
- Heating Elements: Kanthal A1 / SiC / MoSiâ‚‚
- Temperature Accuracy: ±1 °C
- Temperature Uniformity: ±3 °C across heated zone
- Controller: Digital PID with programmable ramp/soak profiles
- Insulation: High-efficiency ceramic fiber insulation
- Mounting: Vertical stand with adjustable height and sample holder support
    Vertical tube furnaces can be customized with the following features:
- Tube Size & Material: Based on chemical compatibility and temperature requirements.
- Gas Flow System: Integrated gas inlet/outlet ports with flow meters or mass flow controllers.
- Vacuum Compatibility: Optional vacuum flanges and sealing systems.
- Data Logging & Connectivity: USB, RS-485, or Ethernet for real-time monitoring and control.
- Software Integration: Compatible with lab automation platforms for programmable thermal cycles and remote operation.
- Optical Access: Optional quartz windows for visual or spectroscopic monitoring.