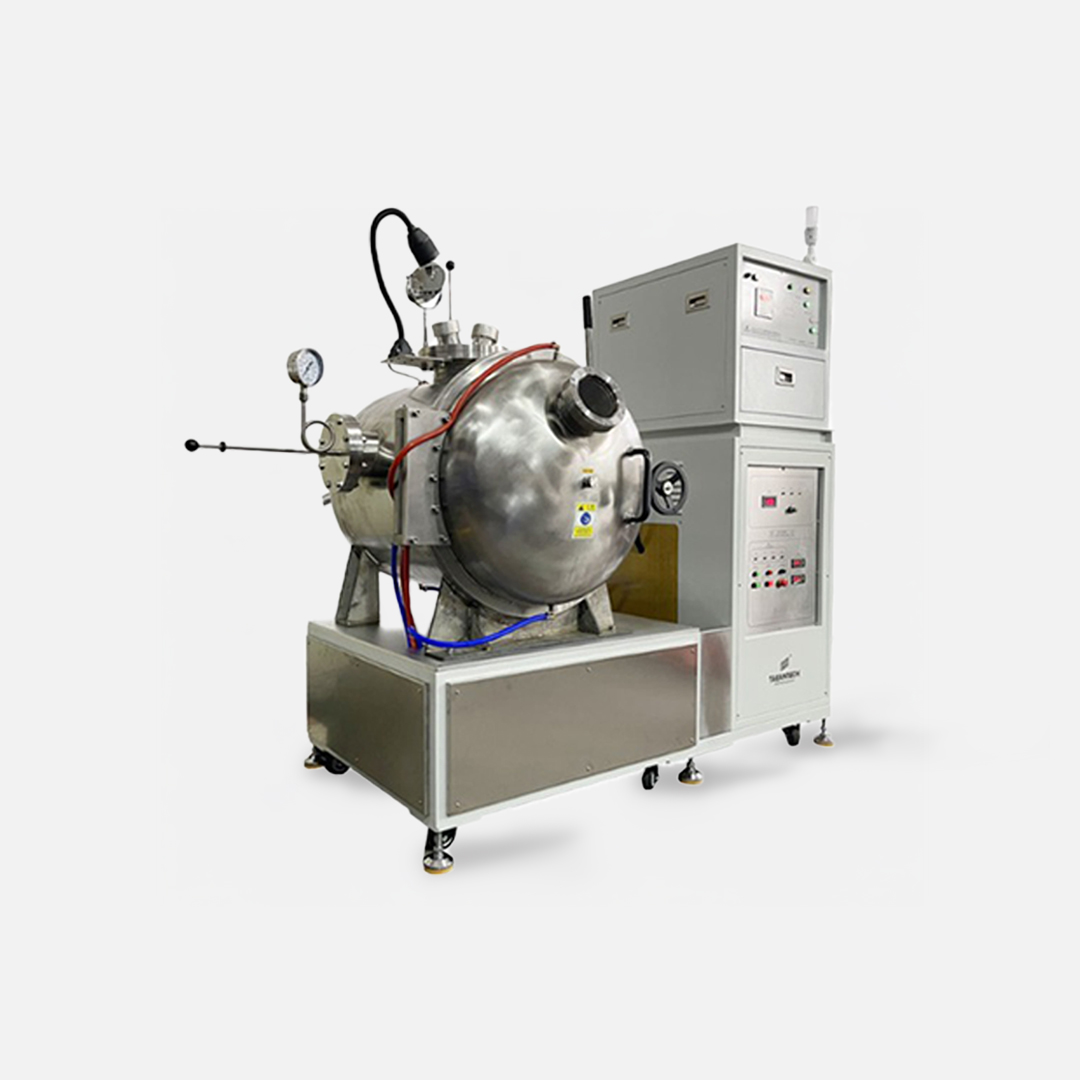
Vacuum Induction Furnace
Vacuum Induction Heating Furnace is a state-of-the-art solution for high precision thermal applications requiring clean, controlled environments. Operating on the principle of electromagnetic induction, this furnace generates heat directly within the material using alternating magnetic fields, ensuring rapid, uniform, and contact-free heating. When combined with vacuum or inert gas atmospheres, it becomes ideal for processes that demand minimal oxidation, contamination-free results, and precise thermal control. Designed for research, aerospace, electronics, and advanced material processing, this furnace integrates customizable configurations and real-time analytical capabilities for in-situ monitoring of material transformations.
- Induction Heating Technology: Efficient, non-contact heating with deep penetration and rapid thermal response, ideal for conductive materials.
- Vacuum & Atmosphere Control: Operates under high vacuum or inert gas environments to prevent oxidation and contamination during heating.
- Smart Control System: Microprocessor-based PID controller with programmable profiles for precise time-temperature management.
- In-Situ Monitoring Integration: Optional ports and interfaces for integrating pyrometers, spectrometers, or cameras to observe material changes during heating.
- Tilting Mechanism for Melt Collection: Motorized or manual tilting of the crucible chamber, which enables safe and controlled pouring of molten material for safe recovery. This system Ideal for casting, alloying, and sample collection.
- Customizable Design: Chamber size, coil configuration, vacuum level, and control interfaces can be tailored to specific process requirements.
- Â Heat Treatment of Metals: Ideal for annealing, brazing, sintering, melting and hardening under vacuum or inert gas.
- Crystal Growth & Semiconductor Processing: Suitable for high-purity applications requiring contamination-free environments with directional and localized heating.
- Â Advanced Material Research: Enables controlled heating and real-time analysis of phase transitions, grain growth, and other material thermal behaviors.
- Â Degassing & Purification: Removes volatile components from materials in a clean, controlled setting.
- Power Range: 10 kW to 100 kW
- Frequency Range: 2 kHz to 20 kHz (model-dependent)
- Capacity: 1-50 kg (depend on power & frequency)
- Vacuum Level: up to 5×10-5 mbar (with appropriate pump configuration)
- Chamber Volume: Customizable from 20 to 500 liters
- Temperature Range: Ambient to 2000 °C (depending on coil and material)
- Heating Coil: Copper induction coil with water cooling; customizable geometry
- Controller: Microprocessor-based PID with up to 4 programmable profiles, each with 5 steps
- Cooling System: Integrated water-cooled system or external heat exchanger
- Monitoring Interfaces: RS485, USB, Ethernet; optional integration with PLC, SCADA, or lab software
- Safety Features: Over-temperature protection, vacuum interlock, emergency shutoff
- Real-Time Monitoring & Feedback: Enables dynamic adjustment of heating parameters based on live sensor data.
- Process Automation: Supports automated heating cycles with programmable ramp rates, dwell times, and cooling profiles.
- Modular Expansion: Optional add-ons include gas purging systems, vacuum bake-out modules, and high-temperature crucibles.
- Safety & Compliance: Equipped with over-temperature protection through thermistor, vacuum interlocks, emergency shutoff, and compliance with CE/ISO standards.