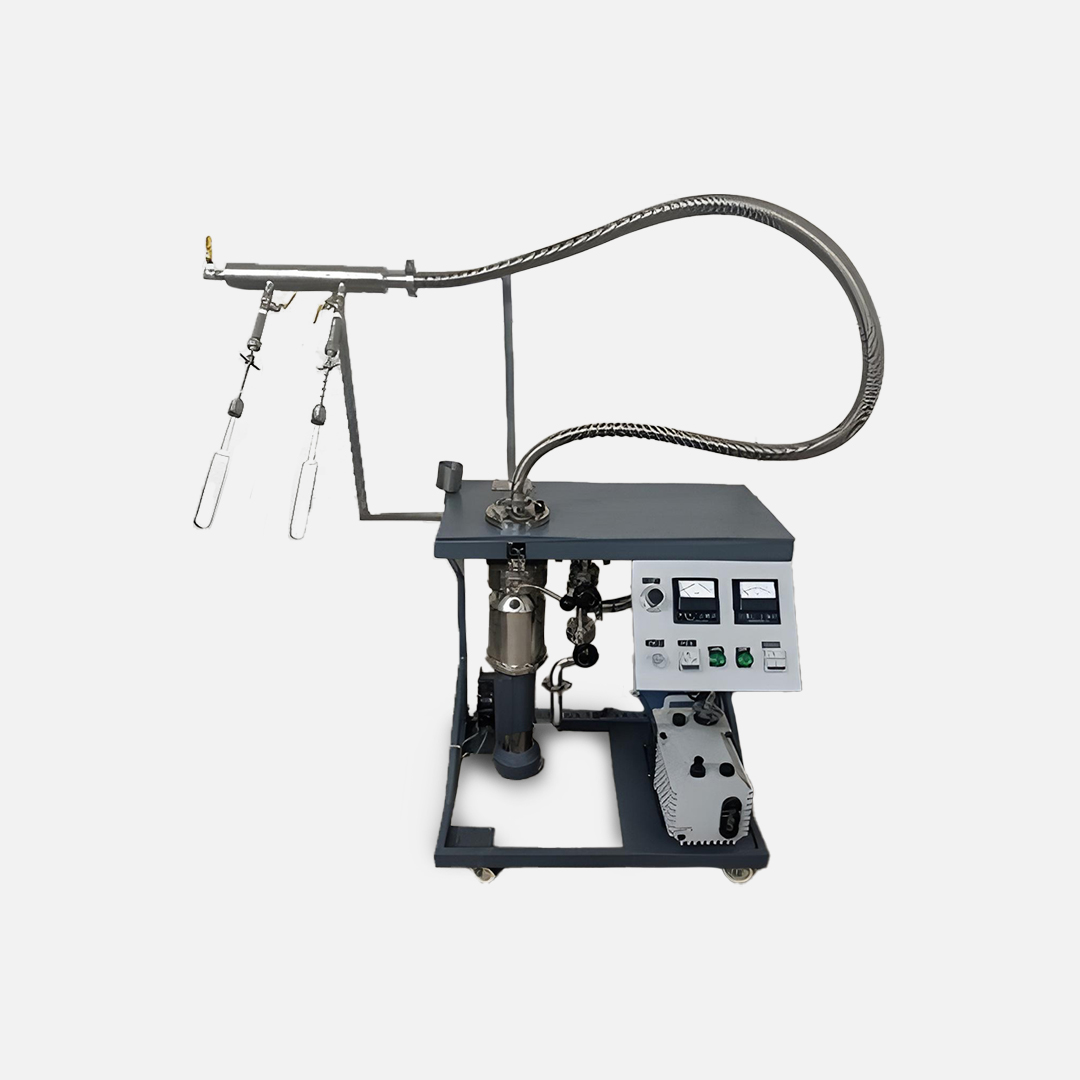
Vacuum Tube Sealing Systems
Vacuum tube sealing systems are essential tools for researchers ,scientists, and manufacturers working with vacuum tubes, gas-filled tubes, and other sealed devices. These systems provide precise and reliable sealing of glass or metal tubing, ensuring the integrity of vacuum or gas environments. Our range of vacuum tube sealing systems offers a variety of solutions for diverse applications, from research and development to production and manufacturing.
Our vacuum tube sealing systems typically consist of a vacuum pump, a sealing station, and associated controls. The sealing station may incorporate a variety of techniques, such as flame sealing, pinch-off sealing, or cold welding, depending on the specific application and materials being used. The system is designed to create a leak-free seal while maintaining the desired vacuum level or gas composition within the tube.
- Precise and Reliable Sealing: Ensure leak-free seals for vacuum and gas-filled tubes.
- Vacuum or Gas Control: Maintain precise control over the internal environment of the tube.
- Versatile Sealing Techniques: Accommodate various sealing methods, including flame sealing, pinch-off sealing, and cold welding.
- Customizable Configurations: Tailored to meet specific tube sizes, materials, and application requirements.
- User-Friendly Operation: Designed for easy setup and operation.
- Durable Construction: Built with high-quality materials for long-lasting performance.
- Safety Features: Equipped with safety features to protect operators and equipment.
- Wide Range of Applications: Suitable for diverse industries and research fields.
   Types of Vacuum Tube Sealing Systems:
- Flame Sealing Systems: Utilize a flame (typically a gas torch) to melt and seal glass tubing.
- Pinch-Off Sealing Systems: Employ a mechanical pinch-off mechanism to seal metal tubing.
- Ampule sealing: The process of sealing glass ampules, which are small sealed vials typically used for storing chemicals, pharmaceuticals, and other substances.
- Research and Development: Sealing custom tubes for experiments and prototypes.
- Pharmaceutical and Biotech: Sealing vials and other containers.
Â
   Customization Options:
- Tube Holders and Fixtures: Custom-designed holders for various tube sizes and shapes.
- Gas Handling Systems: Precise control and metering of gases.
- Vacuum Pumps: Different vacuum pump options to meet specific vacuum requirements.
- Control Systems: Manual or automated control systems for precise sealing processes.
- Tube Diameter Range: 30mm-60mm
- Vacuum Level: 10-1mbar to 10-6mbar
- Vacuum Pump: Single Stage Rotary Pump/ Two Stage Rotary Vane Pump/ Diffusion Pump/ Turbo Pump
- Vacuum Pump Type: Oil Based or Dry Pump
- Pressure Guage: Pirani/Penning Guage
- Sealing Method: Flame Sealing
- Material Compatibility: Quartz
- Number of Ports: 2, customisable as per the requirement
    Safety Considerations:
- Proper Training: Emphasize the importance of proper training and understanding of vacuum and gas handling techniques before using vacuum tube sealing systems.
- Safety Equipment: Always use appropriate personal protective equipment (PPE), including safety glasses and gloves.
- Flammable Materials: Take precautions when working with flammable gases or materials.
- Vacuum System Maintenance: Regularly inspect and maintain vacuum systems to prevent leaks and ensure safe operation.
   Safety:
- Thermostat switch protects diffusion pump from excessive heating.
- Â DP is interlocked with Rotary Pump.
- Â Electrical overload switch.
- Â Rotary pump, Diffusion Pump etc. wired through sensitive circuit breakers.
- Â Overload protection for Rotary pump meter through current switch fixed on the motor