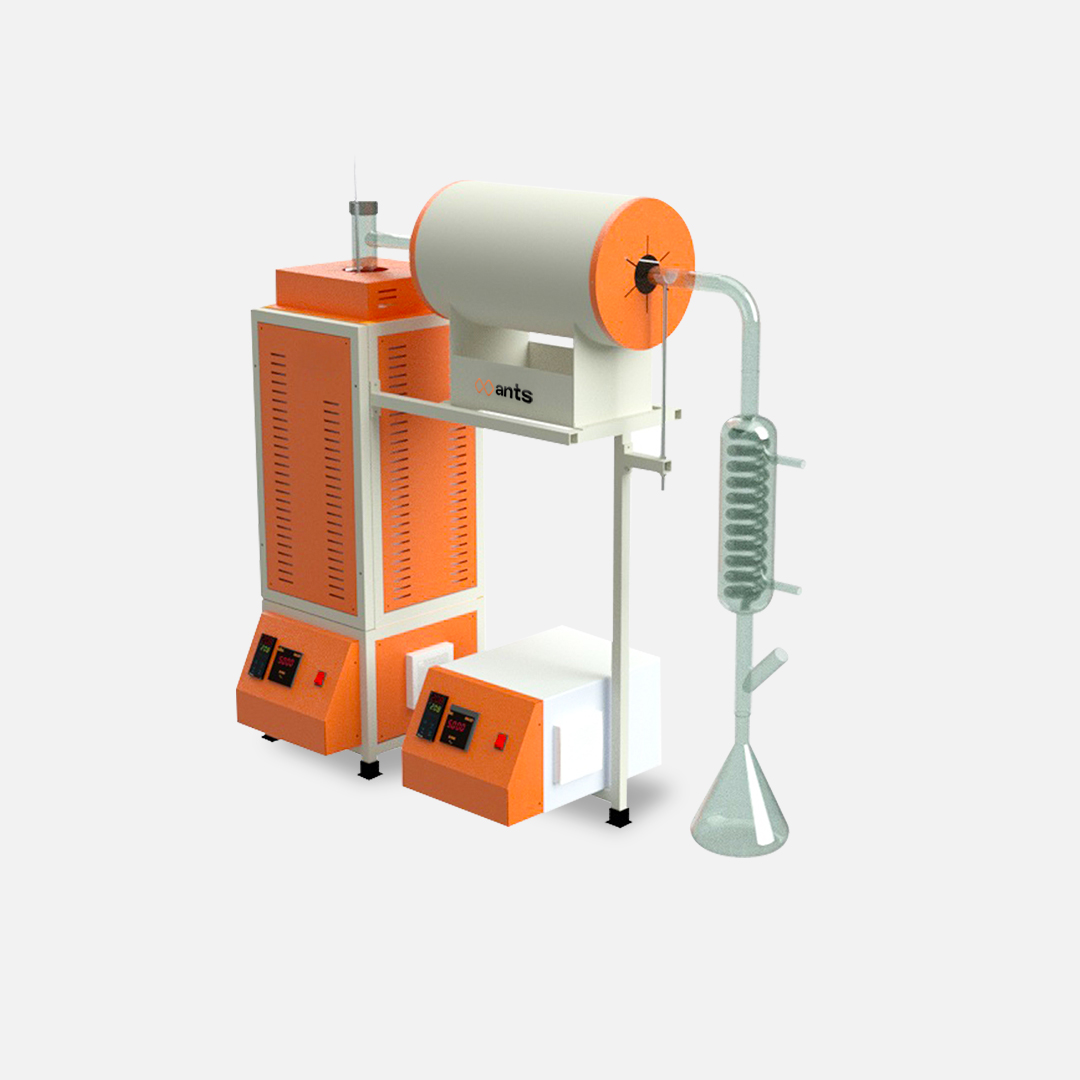
Hydrogen Reduction
Tube Furnace
The Hydrogen Reduction Tube Furnace is engineered for high-temperature processes involving hydrogen or cracked ammonia gas, with a robust safety architecture and reliable performance at temperatures up to 1600°C. These furnaces are ideal for hydrogen reduction, sintering, debinding, annealing, and various thermal treatments in a reducing atmosphere.Â
Optimized for Hydrogen Safety & Performance
Each furnace is designed with leak-tight ceramic tube assemblies, automated purge systems, and optional vacuum pre-treatment for oxygen removal—ensuring the safe and controlled handling of flammable gases. Customization options allow users to choose tube materials, dimensions, and pressure or vacuum systems based on specific process needs.Â
Production-Scale Hydrogen Tube Furnaces for Tungsten/Molybdenum
Ants also offers fully automatic, production-scale hydrogen reduction tube furnaces for continuous tungsten or molybdenum powder reduction. These systems feature:Â
- Automated feeding and dischargingÂ
- Bubbling method discharging controlÂ
- Dual-channel hydrogen control (main + make-up)Â
- Oxygen supply for precise process balancingÂ
- Comprehensive PLC-based automation with alarms, interlocks, and process integrationÂ
Optimized for Hydrogen Safety & Performance
Each furnace is designed with leak-tight ceramic tube assemblies, automated purge systems, and optional vacuum pre-treatment for oxygen removal—ensuring the safe and controlled handling of flammable gases. Customization options allow users to choose tube materials, dimensions, and pressure or vacuum systems based on specific process needs.Â
- Max Operating Temp: Up to 1600°C (For >1800°C, cold wall models are recommended)
- Tube Configuration: High-purity ceramic tube with water-cooled, gas-tight flanges
- Atmosphere Control:
- Inert gas purging (Nâ‚‚/Ar)
- Optional vacuum pump for pre-purge
- Hydrogen/NH₃ gas flow with MFC-based automation
- Safety Systems:
- Hydrogen leak sensor with auto-shutdown
- Emergency inert gas flooding
- Heated gas inlet (prevents condensation)
- Hydrogen burning station (afterburner with propane & air)
- Pressure sensors & relief valves
- PLC/HMI with interlocks and alarms
- Touch Panel Interface with recipe programming
- Real-time Monitoring of temperature, gas flow, pressure, and leaks
- Data Logging & Safety Interlocks included as standardÂ
- Hydrogen Reduction of metal oxides (e.g., Tungsten, Molybdenum)
- Annealing & Sintering in reducing atmospheresÂ
- Metal Injection Moulding (MIM) & Ceramic Injection Moulding (CIM) debindingÂ
- Degassing, Drying, Pyrolysis, Sublimation, Brazing, Quenching, and TemperingÂ
- Rapid Prototyping & Component Testing under controlled hydrogen flow