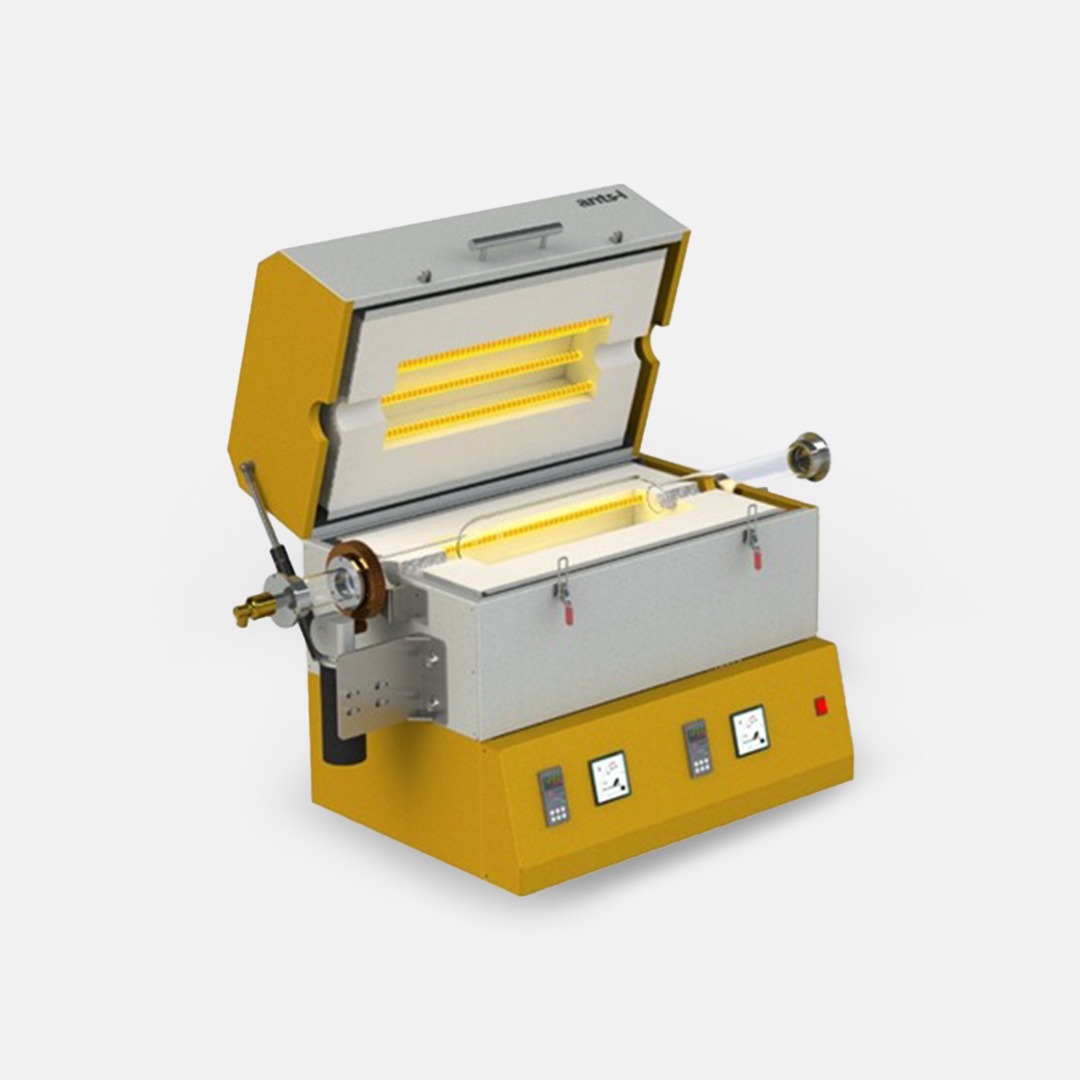
Rotary Tube Furnace
Designed to quickly heat treat the materials in a circular, revolving hearth arrangement, a rotating hearth furnace (RHF) can be designed as a batch type and high-capacity, continuous thermal processing equipment.
A rotary tube furnace is suitable for the heat treatment of granular or particulate materials that continue to flow at high temperatures. Materials that need to be processed in either air or inert atmospheres are suitable. Materials that become sticky at high temperature are not suitable.
It is extensively employed in gaseous reduction of ores and analysis of ores and metallurgical slags, synthesis of: catalysts; pigments for paints; calcination of oil slate; doping of ceramics with rare earth metals and synthesis of battery materials.
The continuous movement of the sample ensures that the entire surface area is exposed to the atmosphere during processing. This improves gas diffusion whilst reducing gas consumption, and increases heat treatment efficiency, when compared to a static processes. RHFs are perfect for demanding industrial environments because of their precise temperature control, high throughput, and energy efficiency.
- Rotating Hearth Design: Ensures uniform heating and efficient material handling with continuous rotation of the workpieces.
- High Throughput: The time taken for material to pass through a rotary tube furnace is widely adjustable. Capable of processing large volumes of material with minimal downtime.
- Multi-Zone Heating: Independent temperature zones allow for customized thermal profiles across the hearth.
- Atmosphere Control: Supports inert, reducing, or oxidizing atmospheres for specialized heat treatment processes.
- Energy Efficiency: Optimized insulation and heat recuperator can reduce energy consumption.
- Metal Reheating: Ideal for billets, blooms, and slabs prior to forging or rolling.
- Heat Treatment: Used for annealing, normalizing, and stress relieving of ferrous and non-ferrous metals.
- Powder Metallurgy: Supports heat treatment of metal powders and granules.
- Waste Reduction: Effective in thermal treatment of hazardous or industrial waste materials.
- Temperature Range: 900 °C to 1300 °C
- Hearth Diameter: 100mm to 1000 mm (custom sizes available)
- Heating Elements: Gas-fired burners / Electric resistance heaters
- Temperature Accuracy: ±5 °C
- Temperature Uniformity: ±10 °C across hearth zones
- Controller: PLC or microprocessor-based system with programmable temperature zones
- Insulation: High-density refractory lining and ceramic fiber insulation
- Rotation Speed: Adjustable via motorized drive system
- Loading Mechanism: Manual or automated loading/unloading systems
   Rotary hearth furnaces can be customized with the following features:Â
- Hearth Size & Configuration: Based on production capacity and material type.
- Atmosphere Control System: Integrated gas injection and exhaust systems for precise environment regulation.
- Automation Options: Robotic loading/unloading, conveyor integration, and real-time monitoring.
- Data Logging & Connectivity: Ethernet, USB, and wireless options for process tracking and remote diagnostics.
- Software Integration: Compatible with industrial control systems for automated operation and analytics.