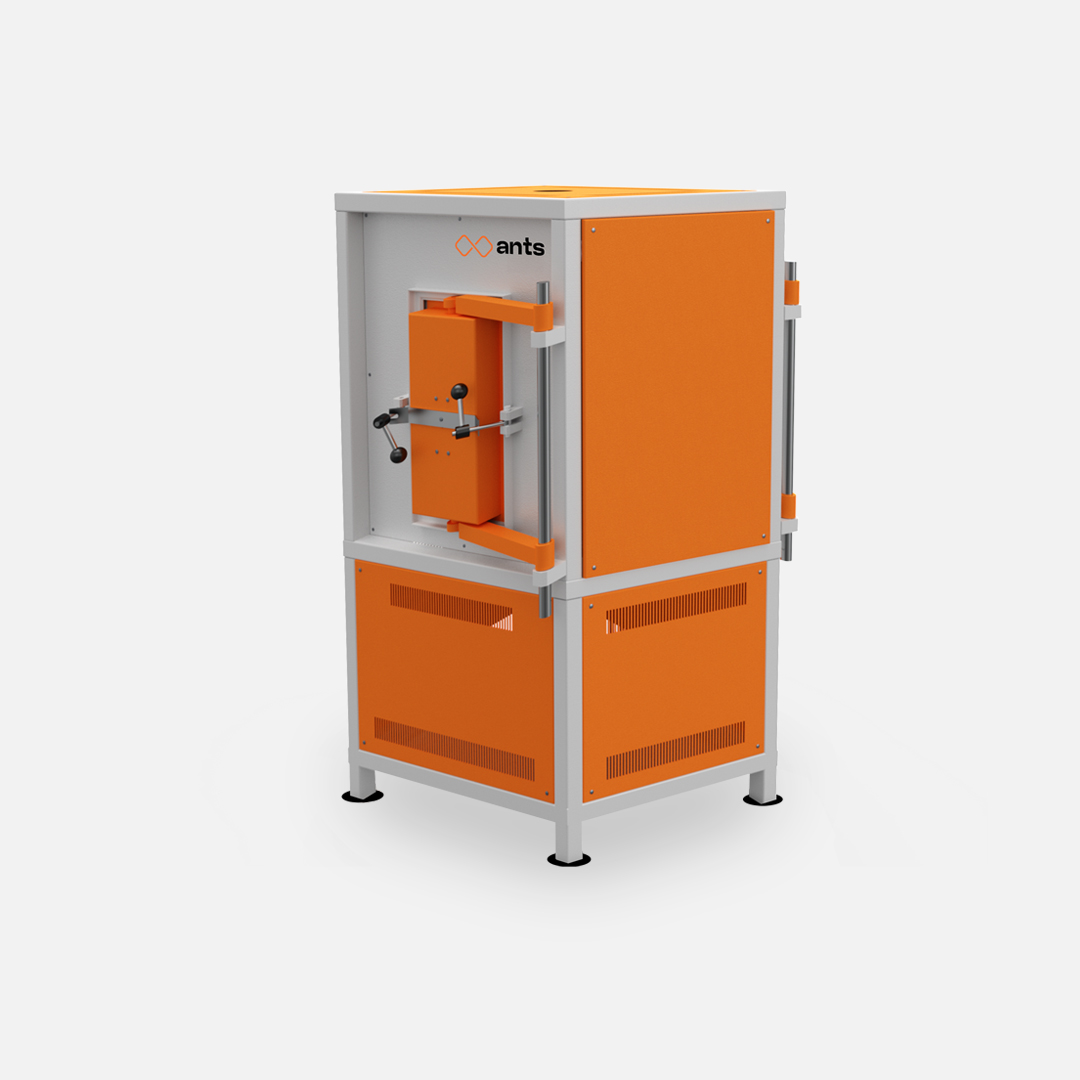
Coke Oven
The Antsprosys Coke Oven Furnace is engineered for the controlled conversion of coal into high-carbon coke, a vital fuel and reducing agent used extensively in steelmaking, ferroalloys, and foundries. Operating in a low-oxygen environment at temperatures up to 1300°C, the system removes volatile components from coal through pyrolysis, leaving behind a porous, carbon-rich solid—metallurgical coke.Â
Built for laboratory and pilot-scale applications, the 7 kg coke oven delivers reliable performance for coal testing, coke yield evaluation, and hot strength assessments using CSR (Coke Strength after Reaction) and CRI (Coke Reactivity Index) methods.Â
Customization Options
The system can be tailored to suit user-specific requirements—from oven size and heating configuration to gas recovery and automation level. This flexibility enables alignment with feedstock type, desired coke quality, scale of operation, and environmental compliance goals.Â
- Triple-Zone Heating: Independently controlled zones with low thermal mass insulation for uniform temperature distributionÂ
- High-Temperature Operation: Up to 1300°C with programmable heating cyclesÂ
- Cycle Time: Efficient carbonization cycle of ~1.5 hoursÂ
- Byproduct Handling: Configurable for collection of tar, coke oven gas, and condensatesÂ
- Data Logging: Optional integration with software for real-time monitoring and analysisÂ
- Atmosphere Control: Inert or reducing environments for clean and consistent cokingÂ
- Integrated Steel Plants – for blast furnace cokeÂ
- Foundries & Ferroalloy Units – requiring high-strength cokeÂ
- Chemical Industry – for by-product recovery and synthesisÂ
- Research Institutions – for coal behavior studies and quality benchmarkingÂ